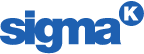
Sigma K provides four practical training courses covering different aspects of Fatigue and Damage Tolerance Training:
A two module Fatigue and Damage Tolerance training course aimed at Stress Engineers, Repair/Design Engineers, Compliance Verification Engineers and Licensed Aircraft Engineers that shows how fatigue and damage tolerance theory is applied to typical aircraft structures. The emphasis throughout is on doing the calculations: what needs to be understood; how the theory relates to practice; what to watch out for; why certain approaches are taken.
Starting with a review of the fundamentals, the first module shows how the certification calculations are carried out and reported, how the common computer programs work and emphasizes the importance of an appropriate inspection method. The second module provides in-depth coverage of more advanced topics such as the derivation of loading spectra, the fatigue and fracture mechanics of joints, stiffened panel analysis and how typical details are analysed, with the emphasis on how the calculations are carried out in reality. Numerous class problems using both British and SI units are used to reinforce the presentation material. A wirebound copy of the slides is included with each Module, and a copy of 'Practical Airframe Fatigue and Damage Tolerance' is included if the full course is booked.
(Please note the book is no longer for sale - it will still be distributed on courses)
Previous and repeat customers include: BAE SYSTEMS Regional Aircraft, Goodrich Aerospace, Atkins, Inter-Tec, ASSYSTEM UK, Spirit AeroSystems, Airframe Designs, Australian Civil Aviation Safety Authority, Cranfield Aerospace, RUAG Technology, Aabsolute Analysis, BAE SYSTEMS Operations, 7Jazi Aerospace, UTC Aerospace Systems, Royal Navy, MoD, GKN Aerospace, eStress, Beechcraft Berlin, PFW Aerospace, Vęzkumnę a zkusební leteckę ústav a.s, Morson Projects, TAI, Klos Aerospace, AERO, EASA, Meggitt Polymers and Composites, CAA, FTI Engineering Network, STC21, Virgin Atlantic, Aptoz and FACC Operations and Solutions.
Customer Ratings (out of 10) (click here for testimonials):
2009 (8.7) 2010 (9.0, 9.2) 2011 (8.2, 9.2, 9.3) 2012 (9.3, 9.0) 2013 (9.4, 9.4, 9.2) 2014 (9.0, 9.5, 9.0, 9.4, 9.6) 2015 (9.3) 2016 (9.2) 2017 (9.3, 9.3) 2018 (9.5) 2019 (9.5) 2020 (9.4) 2021 (9.6) 2022 (9.8, 9.4) 2023 (9.3, 9.4, 9.5) 2024 (9.6, 9.4)
This course covers the application of damage tolerance to repairs and modifications and is aimed at Stress Engineers, Repair/Design Engineers, Compliance Verification Engineers and Licensed Aircraft/Maintenance Engineers. It begins by considering the regulatory requirements, particularly following the recent FAA AC 120-93 and EASA AMC 20-20 and then provides a brief, working overview of damage tolerance theory. Following a discussion of actions that are advisable before metal is cut, the course covers stop-drilling, the oversizing and spotfacing of holes, the treatment of blends, load transfer through the repair and finally the factors that influence the life of a repair doubler. The inspectability of the repair is considered, together with how to assess the threshold and repeat inspection interval using either RAG/REG documents or by formal analysis, including possible actions that can be taken if data is limited.
Customer Ratings (out of 10):
2009 (9.0) 2010 (8.8, 9.0,9.0) 2013 (9.7) 2022 (9.0)
'Les Bent was an excellent presenter and clearly very enthused and experienced' Ian Cobb, Programme Manager, BAE Asset Management
Previous customers include: BAE SYSTEMS Regional Aircraft, Goodrich Aerospace, Atkins, Inter-Tec, Airframe Designs Ltd, BAE SYSTEMS Asset Management, EDO MBM Technology Ltd, ASSYSTEM UK Ltd and Spirit AeroSystems.
Aimed at Design and Repair Engineers, the presentations give an overview of the fatigue process, the behaviour of different materials and the effect of processing, stress concentrations, load transfer through joints, design rules, interaction of stress concentrations, mitigation against fatigue, an overview of damage tolerance and finally how doublers and reinforcements behave.
Customer Ratings (out of 10):
2012 (9.2) 2013 (9.2)
Customers include: Goodrich Aerospace, BAE SYSTEMS Regional Aircraft
Aimed at Production and Line Supervisors, Mechanics and Fitters, the presentation shows why commonly occurring concession or repair details matter in terms of the strength and durability of a structure. Over twenty five commonly occurring discrepancies, including mis-located holes, blends and shims, are covered in detail by means of over sixty finite element models. The examples are illustrated by means of stress contours and vector plots along with an estimate of the effect on the fatigue life of the structure, giving an immediate and lasting visual feedback and proving the old adage that a picture is worth a thousand words. The presentation is a cost and time effective way of giving your production staff a great insight into how their work affects the fatigue life of the structure.
Repeat customers include: Spirit AeroSystems, Goodrich Aerospace, Fleet Forward Support (Air) MASU
Please click here for examples from this course
All of these courses can be customised to your own requirements.
For costs, further information on course content or to discuss your specific training requirements please email us your enquiry, or phone 07941 125 445 or use our contact form.